The Leak Test Apparatus is used primarily for the leakage testing of food, drug, and other industrial pharmaceutical products.
It is a very essential equipment to test the quality of packing processes in strips, blisters, and sachets containing tablets, granulates, and liquids. Also, it ensures seals enclosing the product are perfectly intact.
Some Leak Tester apparatus work on the principle of creating a negative pressure in a closed chamber which inflates the sealed pouches due to pressure and leaked pouches don’t inflate.
A modern manufacturing line system is designed to deliver a final product with high reliability and always increasing performance.
The leak test apparatus is usually incorporated as one of the methods for process monitoring and quality control: an accurate leak test can surely grant product quality in terms of reliability, performance, and safety.
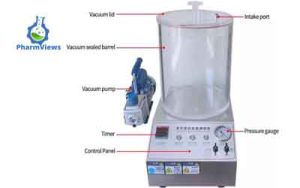
Advantages of leak test apparatus
- To ensure the integrity of checked parts
- Ensure good functionality
- Avoid contamination problems
- Reduce reworking
- Reduce production costs
- Total quality assurance of the parts
How leaks occur
- Porosity
- Flaws/cracks
- Machining errors
- Part defects
- Missing seals
- Defective seals
- Wrong positioning
- Wrong assembling
Leak tester apparatus maintenance
- Leak Inspect the Leak Inspector
- Self-Check of Regulators and Transducers
- Checking Your Probe and Seals for Signs of Wear and Damage
- Change Out Filters to Maintain Dry Air
- Check Your Greasing Points
- Clean Contact Points
- Safety Checks
Leak testing techniques
- Part pressurization and/or water dunk
- Pressure decay measurement:
– by relative transducer
– by differential transducer
- Flow measurement
- Mass Spectrometer for helium
Industries that use leak testing apparatus
- Automotive
- Consumer goods
- Medical Devices
- Packaging
- Sealed Electronics
Leak test apparatus
Below, you will find some of the top examples of the different leak test apparatus, machines and procedures;
Air leakage inspection devices
Air leak testing devices have displays that show inspectors data from ongoing leak tests.
Compact pressure decay leak tester
This kind of compact leak tester can be placed close to fixtures being used in leak testing, allowing inspectors to reduce the amount of connection volume needed for the test.
Leak standard
Inspectors use leak standards to define the parameters of their leak test by creating a simulated leak in the part under test, or to compare multiple leak systems with each other.
Conclusion
The quality of packaging remains of utmost importance because it can produce the quality of the product being packaged. Also, it is usually in the course of packaging that the leak tester apparatus comes into play.
No matter the quality of a product, once there is leakage, the product has the tendency of losing its value which is why testing for leakage remains a priority.
Reference
Editor’s Picks
Manual Tube Filling Machine; types, operation, advantages, disadvantages